Shore hardness explained compactly
Term, scales, methods and more information.What is Shore hardness?
Shore hardness is a key figure that got invented to make the hardness of different materials comparable. It mostly gets used for the comparison of rubber or plastics. The key figure was established by the American metal scientist Albert Ferdinand Shore. In 1915, he invented the square durometer with which he was able to determine the hardness of polymers and elastomers.
To put it simple: The higher the key figure, the harder is the measured material. However, there are several different scales that are not linearly convertible into each other.
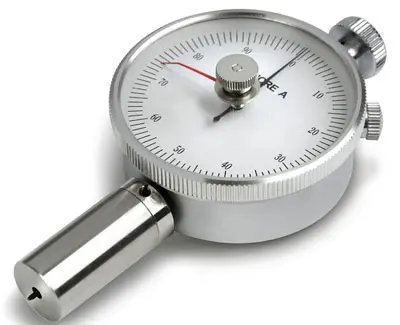
Which Shore hardness scales exist?
There are a bunch of different scales to depict the Shore hardness of different materials. Each scale differs from the others by its measurement method. Hence, even though the scales might overlap partially, it is not possible to convert them into each other linearly. If someone wants to depict a given Shore hardness on a different scale, it is advisable to use a comparison table.
Within the rubber and plastics industry, the scales Shore A and Shore D are the most common. The letter for the labelling of the scale usually gets included in the specification of the measured value so that everybody can immediately see which scale is used. The values could look as follows:
- 98 Shore A – for hardness of 98 on the Shore A scale
- 54 Shore D – for hardness of 54 on the Shore D scale
Everyday examples for Shore hardnesses
Shore hardness | Object |
10-15 Shore 00 (below the Shore A scale) | Gummy bears |
30-35 Shore 00 (below the Shore A scale) | Gel shoe insoles |
25–30 Shore A | Rubber bands |
40–45 Shore A | Eraser |
65-70 Shore A | Car tires |
90-95 Shore A | Shopping cart wheels |
80 Shore D (above the Shore A scale) | Safety helmet for cunstrucion sites |
The Shore A scale
This scale typically is used for softer plastics such as soft polyurethanes or silicone. The lower end of the scale (0 Shore A) equals gel-like materials. At the upper end of the scale, more solid plastic materials such as shopping cart wheels (90 – 95 Shore A) can be found. As all Shore scales, the Shore A scale ends at 100. Consequently, harder materials get depicted on the Shore D scale.
The Shore D scale
This scale usually is used to measure the hardness of more solid plastics such as harder polyurethanes or polyamide. As already mentioned, there are some overlaps with the Shore A scale. Values below 50 Shore D are depicted on the Shore A scale in most cases despite it would be possible to locate them on the Shore D scale as well.
Further Shore scales
The hardness of most materials gets depicted on the Shore A and Shore D scales described above. Nevertheless, there are even more scales (and hence, more measurement methods), to illustrate the hardness of especially hard materials or those who fall in between Shore A and Shore D hardness. Here is an excerpt of further Shore scales:
- Shore 00: For especially soft materials
- Shore 0: For soft plastics – the scale has a relatively large cut quantity with Shore A
- Shore B: located in between Shore A and Shore D
- Shore C: located in between Shore A and Shore D – harder materials than Shore B
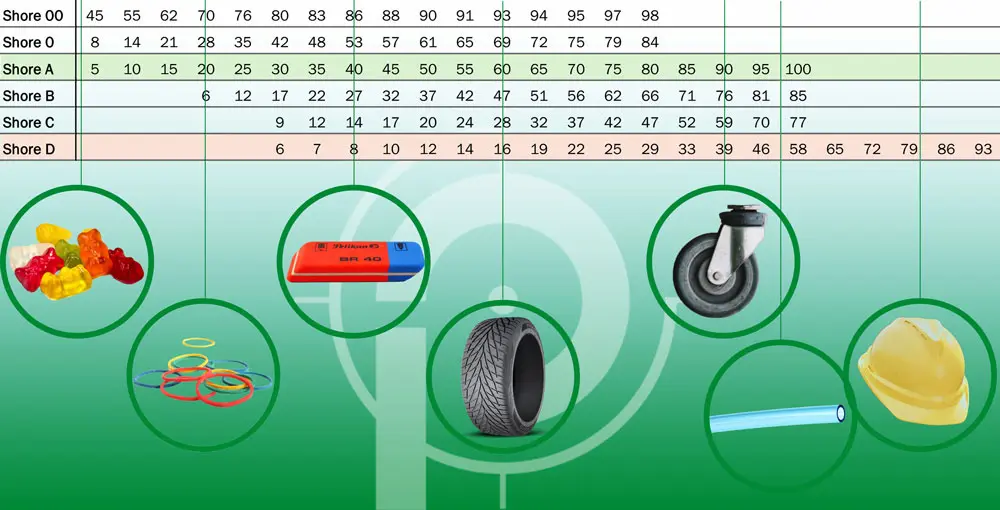
How is the Shore hardness measured?
The tool to measure the Shore hardness is called durometer. During the usage of a durometer, it is measured how deep a precisely defined object, a so called indenter, that is located at the end of the durometer, can penetrate the measured material.
The indenters differ at the various measurement methods linked with the Shore scales described above. Moreover, the pressure used during the measurement is different as well.
Rules for measuring Shore hardness
Since it is tested how deep an indenter can penetrate a material with a certain load, it is important to create appropriate conditions for these tests. Firstly, it has to be ensured that the material gets tested on a solid surface. If the surface would give way during the measurement, the result would be artificially low. The second point to mention is the temperature of the tested material. Most materials change their hardness relative to temperature. Some fabrics might stay unchanged in during common temperature undulations. However, other substances, such as thermoplastic polyurethane, change their hardness even during these everyday alternations. As a result, it is even more important to test the Shore hardness of such temperature sensitive materials under constant conditions.
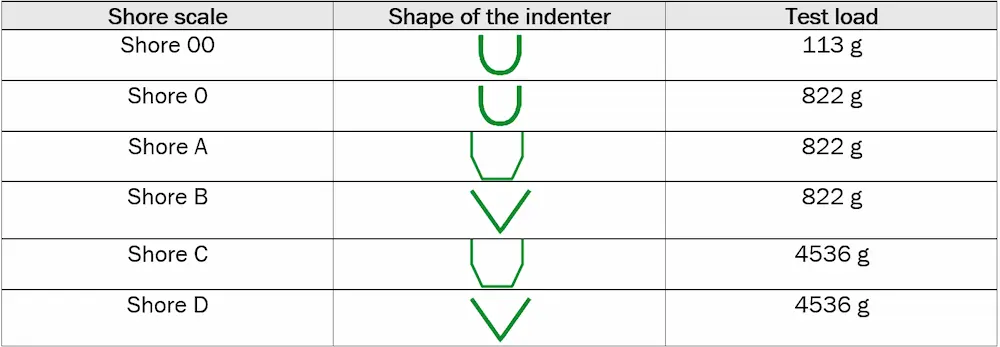
Valid norms
Whoever wants to determine the Shore hardness of a material precisely should do that according to one of the current norms. These norms regulate many other circumstances that can influence the measurement, such as:
- Sample thickness
- The number of sample layers
- The number of measurements
- The distance between measurement points
Examples for current norms to determine the Shore hardness:
- ASTM D2240: This norm published by the American Society for Testing and Materials (ASTM) bears the title “Standard Test Method for Rubber Property – Durometer Hardness”. It regulates the methods for determining the Shore hardness of elastomers.
- ISO 868: This norm published by the International Organization for Standardization (ISO) bears the title “Plastics and ebonite — Determination of indentation hardness by means of a durometer (Shore hardness)”. It describes the method to measure the Shore hardness of plastics and ebonites (special forms of hard rubber).
Shore hardness of TPU (thermoplastic polyurethane)
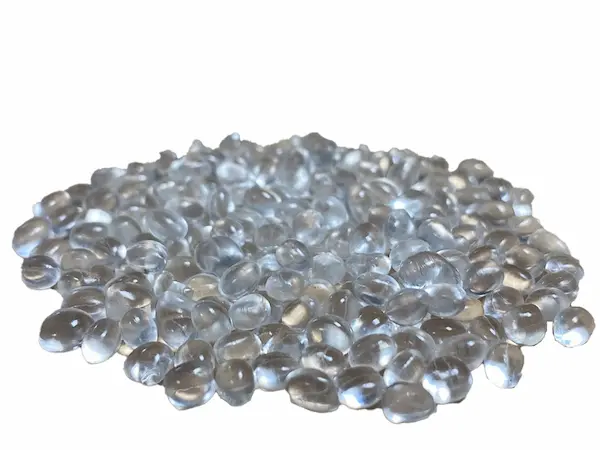
TPU is available in a variety of Shore hardnesses. They range from medium soft (60 Shore A) to hard (70 Shore D). The different hardnesses fulfill varying demands in various applications. For example, softer TPU gets used for seals and handles. On the other hand, harder TPU has its use cases mostly in industrial applications or even shoe soles. It is crucial to chose the correct TPU with an appropriate Shore hardness because the different degrees of hardness promote completely different application areas. The same is true for the products made of the versatile material, for example pneumatic tubing. Here, the Shore hardness is decisive for pressure resistance and hence, for the bursting pressure as well.
Summary
The Shore hardness is a key figure which enables to depict the hardness of different materials. The higher the number, the harder is the tested material. There are several scales for the Shore hardness. Within plastics industry, the usage of Shore A and Shore D scales is most common. Usually, the scale is mentioned when displaying the Shore hardness by putting the letter behind the measured number.
The instrument to measure Shore hardness is called durometer. During the measurement process, a precisely defined indenter penetrates the measured material. By means of the penetration depth, the Shore hardness is calculated. To receive more precise results, a hard measurement ground and constant temperature are crucial. Optimal result can be achieved by following the valid norms.
Any questions?
Don’t hesitate to give us a call – we are happy to advise you.