Extrusion as a process technology
Extruder design, applications, techniques.Extrusion explained in a nutshell
The name extrusion comes from the Latin word extrudere, which means “to push out” or “to expel”. This already explains the basic principle of extrusion: a raw material is heated and then pressed out through a shaping opening. For this reason, materials that can be softened by heat so that they can be pressed into the desired shape are mainly suitable for extrusion. In addition, these materials must also harden again after heating and cooling so that they remain in the new mold. In the case of plastics, such materials are called thermoplastics. The result of this process is called an extrudate. The machine used for extrusion is called an extruder.
Today, extrusion is one of the most important process technologies for seamlessly converting raw materials into a desired shape. The beginnings of process engineering date back to 1795, when the British engineer Joseph Bramah developed a machine to produce seamless lead pipes. Since then, the process has developed enormously and is used in various designs and diverse industries.
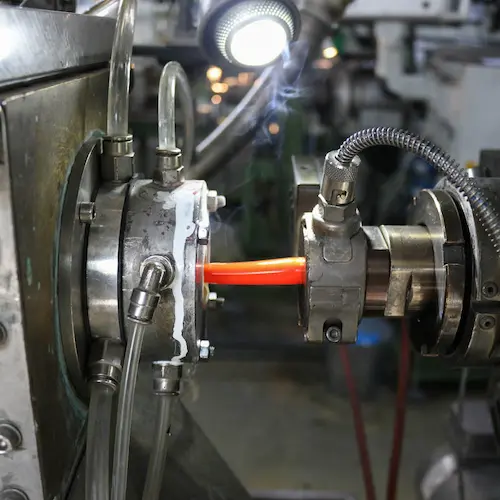
Design and types of extruders
Screw extruder
Screw extruders are probably the most common type of extruder. In a screw extruder, the material is fed onto a screw conveyor that passes through various heating zones. While the screw conveyor transports the processed raw material to the front, it is heated in the heating zones and thus softened. Finally, the screw presses the heated material out of the shaping opening and the extrudate is hardened in the desired shape by cooling, which usually takes place in a water bath. For many applications in the plastics and food industries, the simple, robust, and comparatively inexpensive single-screw extruders are the most efficient alternative.
In addition to simple single-screw extruders, which, as the name suggests, only have one screw conveyor, twin-screw extruders are also frequently used. In twin-screw extruders, two screw conveyors run simultaneously, either counter-rotating or co-rotating, to convey the material toward the opening. The main advantage of twin-screw extruders is that the conveyed material is better mixed. Accordingly, they are mainly used for materials that are difficult to mix. In addition, twin-screw extruders ensure a more even material feed compared to single-screw extruders, which can lead to greater process reliability with materials that are difficult to process.

Piston extruder
In a piston extruder, malleable material is also pressed through a shaping opening. However, in this form of extrusion, the raw material is fed into a cylinder in which the piston is located. The material is then conveyed towards the opening by uniform pressure from the piston. Extrusion with piston extruders is primarily used in areas that require high precision. The process is also suitable for raw materials that have to be processed under high pressure.
Screw extruder vs. piston extruder
Both, extrusion with screw extruders and with piston extruders have their advantages and disadvantages. Probably the biggest difference between the two types of extrusion is continuity. While production with screw extruders can continue for a very long time (the lines only have to be shut down for cleaning), production with piston extruders has to be interrupted much more frequently in comparison. The reason for this is simple: the plunger has to be retracted again and again and the barrel refilled with material. With screw extruders, on the other hand, the material can be fed continuously by adding it to the rotating screw.
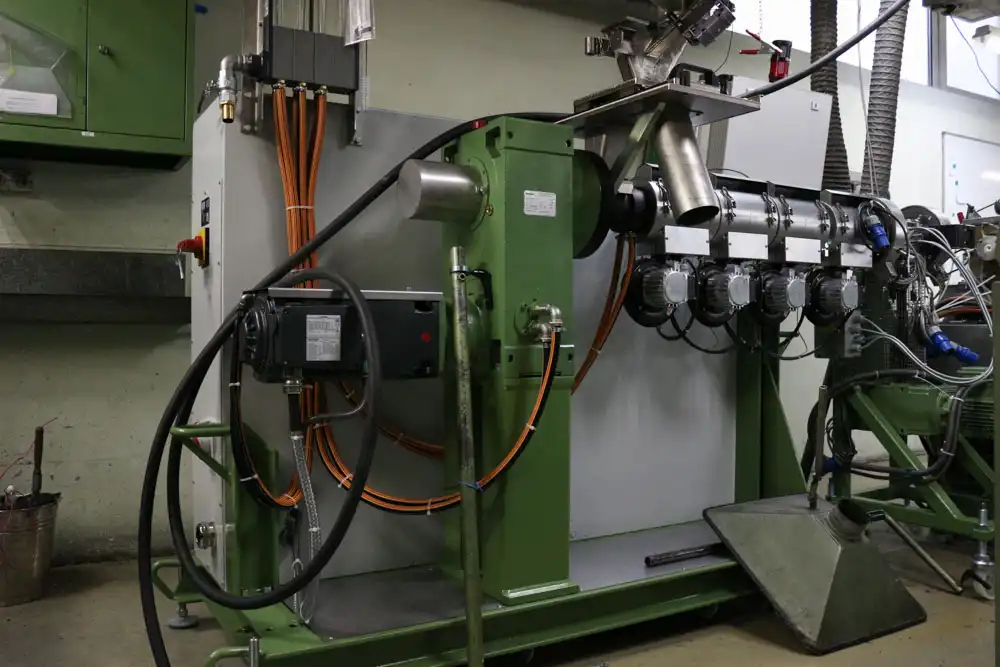
With this method, screw extruders generally achieve a significantly higher material throughput than piston extruders. On the other hand, piston extruders can generate significantly higher pressures than screw extruders, which can be an advantage when extruding some materials. Due to their comparatively simple design, piston extruders are also easier to maintain and clean than the much more complex screw extruders.
While screw extruders additionally mix the processed material during conveying due to the rotary motion, this hardly happens with piston extruders. However, this movement also results in a high material load due to shear forces. Here again, the piston extruder can score points, as these shear forces do not occur and the material is therefore conveyed more gently.
The bottom line is that there is no perfect extruder for all materials. It must be decided on a case-by-case basis which is better suited to the desired result. An overview of the advantages and disadvantages of screw and piston extruders:
Screw extruder | Piston extruder |
+ continuous operation | + Very high pressures |
+ high throughput rate | + precise dosing |
+ versatile usage possibilities | + simple cleaning and maintenance |
+ intense material intermixing | + gentle material treatment |
– complex cleaning and maintenance | – interrupted operation |
– high material strain | – low throughput rate |
– limited usage possibilities |
Various extrusion techniques
In the more than 200-year history of process engineering, various forms of extrusion have been developed to get the maximum efficiency out of every material. The techniques mentioned in the following rough overview cannot always be differentiated from one another and are sometimes used as mixed forms:
Different temperature ranges
Cold extrusion
In cold extrusion, materials are processed at low temperatures, as the name suggests. This process usually takes place at room temperature. However, only materials that are soft enough to take on a new shape at such low temperatures are suitable for cold extrusion. By eliminating the heating process, significant energy savings are possible. On the other hand, due to the harder state of the materials to be processed, significantly more pressure often has to be exerted. As a result, the material wear on the tools is often higher.
Hot extrusion
In hot extrusion, the processed materials are brought to a higher temperature. This is necessary for many materials so that they can be pressed into a new shape in the first place. Compared to cold extrusion, in many cases, significantly less pressure is required to press the material through the die. Hot extrusion takes place below the recrystallization temperature of the processed material. If the material is processed above the recrystallization temperature, it is no longer referred to as warm extrusion, but as “hot extrusion”.
Different pressure variants
Direct extrusion
In direct extrusion, as in most of the examples described so far, a material is pressed through a die to give it its shape. However, this creates friction on the processed material, which in certain cases can hurt the properties of the end product.
Indirect extrusion
The major difference between indirect extrusion and direct extrusion is that the raw material remains firmly in a chamber. Shaping is achieved by the die moving towards the material and pressing it into shape through the opening. This has the advantage of eliminating the friction caused by the raw material sliding towards the die during direct extrusion.
Hydrostatic extrusion
In hydrostatic extrusion, the processed material is not pressed directly through an opening using a piston, but a liquid is added between the material and the piston. This has the advantage that the pressure of the piston is distributed more evenly. In addition, friction is significantly lower due to the use of liquids.
Impact extrusion
In impact extrusion, a short blow from a plunger is used to shape the material. This creates a cavity in the workpiece that is ultimately formed, as the material closes around the punch due to the impact
Areas of application for extrusion
Extrusion in plastics processing
In plastics processing, extrusion is an important process technology for shaping thermoplastics. Thermoplastics are particularly suitable for the production of extrudates, as they become soft and malleable under the influence of heat. This allows them to be pressed perfectly through a die into a specific shape using screws or pistons. The thermoplastics can then be fixed in their new shape by cooling sections. Plastics can also be perfectly portioned for processing in an extruder, often in the form of pellets. Extrusion offers the following advantages in plastics processing:
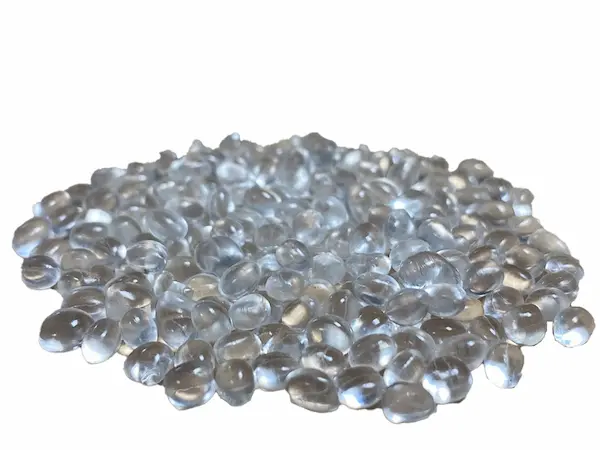
- high process speed: large quantities can be produced without interruptions, especially when using screw extruders.
- material and cost efficiency: because the machines rarely have to be shut down, there is little waste compared to other process technologies for shaping plastics. In combination with the high throughput rates, this also makes extrusion cost-efficient.
- versatility: Using different extruders (the nozzle is particularly important), various shapes can be produced with a high level of process reliability.
Examples of plastic extrudates
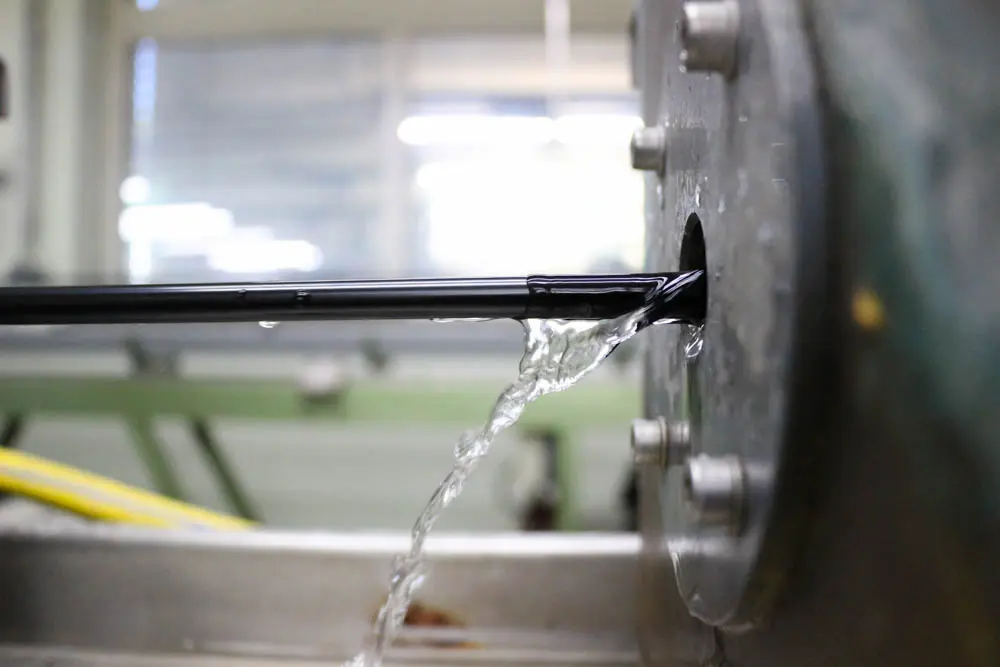
– Tube extrusion: Industrial tubes can be extruded in various shapes. The plastic, in many cases polyurethane or polyamide, is pressed through a die as usual. A so-called mandrel in the middle of the nozzle ensures that the tube remains hollow in the middle. The extrudates produced in this way are often used as pneumatic tubing or for transporting liquid media.
– Film extrusion: In film extrusion, the plastic granulate is pressed through an extremely narrow die (slot die). This allows very thin plastic films to be produced without interruption and wound onto rolls.
– Profile and sheet extrusion: Complex profiles, for example for the construction or furniture industry, can also be produced using extrusion.
– Fiber extrusion: Synthetic fibers for textiles or carpets can also be extruded. To do this, the plastic is pressed through very fine multi-hole nozzles (spinnerets) to produce a large number of fibers at the same time.
Extrusion in metal processing
Extrusion is still used in metal processing today, just as Bramah, who is considered to be the inventor of the process, had in mind. The basic principles of process engineering are similar in plastics and metal processing: the metals are made malleable and pressed into the desired shape through an opening. However, the specific processes differ significantly due to the different physical properties. The processing temperatures alone are significantly higher in metal processing.
Examples of metal extrudates:
– Profiles and rods: aluminum profiles for window frames, door frames, or vehicle construction, for example, can be produced continuously using extrusion.
– Wires: Electrical cables and contacts made of copper are classic extrudates in many cases.
– Pipes: The oldest application of extrusion is still in use today. Tubes made of various metals are extruded. The biggest advantage here is the seamless production.
Extrusion in food technology
Contrary to what one might intuitively assume, extrusion is also often used in the food industry. There are four reasons why extrusion is used in the food industry:
- efficiency: with extrusion, food can be cooked and shaped at the same time, which saves work steps and enables particularly efficient production.
- quality: Thanks to the high process reliability of extrusion, large quantities of food can be produced in a consistent quality.
- nutrient preservation: The cooking and shaping process can be designed for most food extrudates in such a way that the nutrients from the ingredients used are preserved.
- versatility: Extrusion can be used to produce a wide variety of foods.
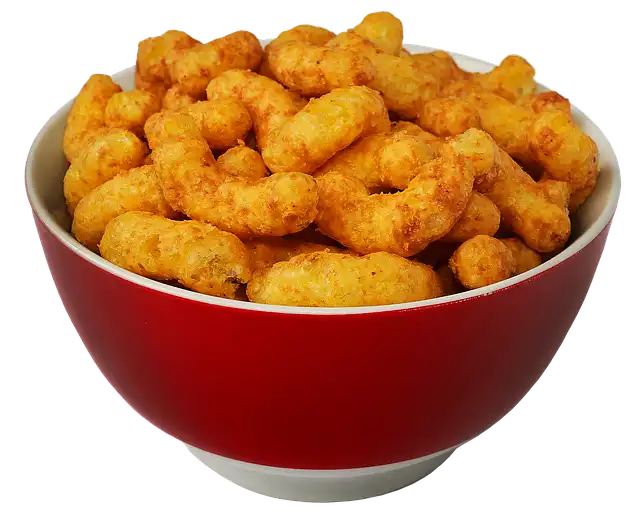
Examples of food extrudates
– Snack products: Chips and flips can be ideally cooked and pressed into shape at the same time using extrusion.
– Breakfast cereals: Breakfast products in various shapes such as cornflakes or puffed rice flakes can also be extruded efficiently.
– Pasta: Noodles in all shapes and lengths can be produced by extrusion using various nozzles.
– Meat substitute products: Vegetarian and vegan products that resemble meat in texture can be produced by extruding textured plant proteins.
– Confectionery: Chewing gum, jelly sweets, and licorice are often given their typical shape using extrusion.
Many of the products that we consume daily are thus given their typical shape using the process that was developed at the end of the 18th century for the production of metal tubes. Both piston extruders and screw extruders in their various forms are also used in the food industry.
Summary
Extrusion was invented as a process technology at the end of the 18th century and has developed enormously since then. Extrusion involves pressing a material through a shaping opening (die) to give it its final shape. The process is used to process various raw materials such as metals, plastics, but also foodstuffs. One of the main advantages of extrusion is that seamless productions can be realized. It also offers a very high level of process reliability and comparatively high material efficiency.
The devices required for extrusion are called extruders. Extruders come in many different forms, each of which has its advantages and disadvantages. The main distinction is between screw and piston extruders. Just as there are different types of extruders, there are also different process designs. For example, there is cold and hot extrusion, as well as direct and indirect extrusion. The bottom line is that process engineering offers an attractive opportunity for various industries to efficiently transform raw materials into the desired shape.
Any questions?
Don’t hesitate to give us a call – we are happy to advise you.