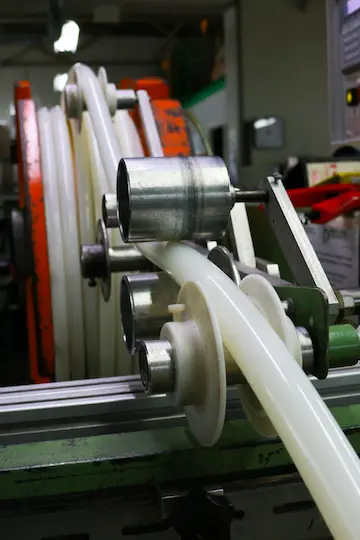
Tube development is extremely important at PAPUREX because as a specialized tubing manufacturer, innovation has always been a priority. Over the course of the company’s more than 40-year history, more than 6,000 article variations have been created. Some of these, such as the KSS anti-kink tubing, are unique to PAPUREX.
The importance of development work is also made clear by the fact that it has been a top priority for over 20 years. The senior managing director, Rudolf Biebl, is currently handing over the reins and management of the development team to his elder son, Ivo Biebl, who has been part of the technical management team since 2024. Tube development is also firmly anchored in the company’s ISO 9001-qualified quality management system.
Tube development is running at full speed
In the first few months of 2025, the PAPUREX development team has already been extensively challenged. True to the company slogan “Individual Tubing Solutions”, even the most demanding customer requests are being realized. If nothing suitable can be found in the tube manufacturer’s product range, a completely new tube is developed.
This was recently the case with a request from a major car manufacturer who needed to transport bolts safely from one machine to the next for its production. This once again demonstrates the versatility of polyurethane as a material, which is by no means only suitable for the production of pneumatic tubing. Thanks to the material’s high abrasion resistance, metal bolts can be shot through a polyurethane tube without any problems – and with minimal wear. This key property, coupled with the other advantages of the plastic, such as good flexibility, was also decisive in the development of the tube for the automotive group.
Large dimensions pose major challenges in development
Tube development in the field of polyurethane extrusion usually takes place between 6 and 16 millimeters in outer diameter. The production of larger dimensions in particular poses considerable challenges. However, in order to be able to convey metal bolts through a tube without jamming, this development project required dimensions beyond 20 millimeters outer diameter. However, this is nothing new for PAPUREX, as the V:S:S® supply system tube, designed for maximum flow in warehouses, already boasts outer diameters of up to 28 millimeters.
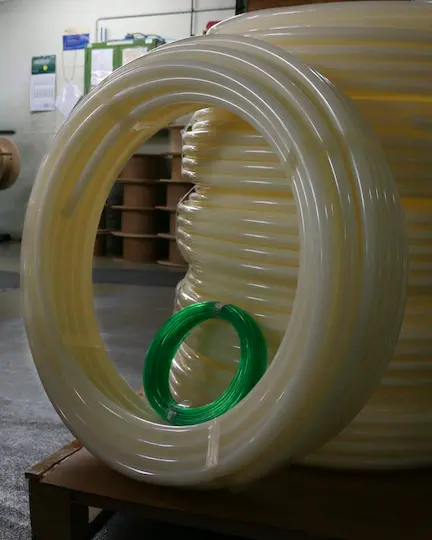
However, size was not everything when developing the new tube for the car manufacturer. Certain sliding properties also had to be ensured so that the bolts could slide smoothly through the interior of the tube. Such a project can only be realized with perfectly coordinated production tools and the right temperature pattern. At this point, the PAPUREX team’s many years of experience in tube development were once again essential.
Do you also have challenging tube development projects on your agenda? Get in touch with our experts now and see PAPUREX’s expertise for yourself.