Extrusion als Verfahrenstechnik
Definition, Methoden, Anwendungsgebiete, Maschinen.Extrusion kompakt erklärt
Der Name Extrusion stammt vom lateinischen Wort extrudere ab, das „Hinausstoßen“ oder „Heraustreiben“ bedeutet. Das erklärt bereits das Grundprinzip der Extrusion: Ein Rohstoff wird erhitzt und dann durch eine formgebende Öffnung hinausgepresst. Aus diesem Grund eignen sich für die Extrusion hauptsächlich Materialien, die sich durch Wärme weich machen lassen, damit sie in die gewünschte Form gepresst werden können. Zudem müssen diese Werkstoffe nach dem Erhitzen bei der Abkühlung auch wieder aushärten, damit sie in der neuen Form verbleiben. Im Fall von Kunststoffen nennt man solche Materialien Thermoplaste. Das Ergebnis dieses Prozesses nennt man Extrudat. Anlog heißt die Maschine, mit der die Extrusion vollzogen wird, Extruder.
Die Extrusion ist heute eine der bedeutendsten Verfahrenstechniken, um Rohstoffe lückenlos in eine gewünschte Form zu bringen. Ihre Anfänge werden auf 1795 datiert, als der britische Ingenieur Joseph Bramah eine Maschine zur Herstellung nahtloser Bleirohre entwickelte. Seitdem hat sich das Verfahren enorm weiterentwickelt und wird in verschiedenen Ausführungen und diversen Brachen verwendet.
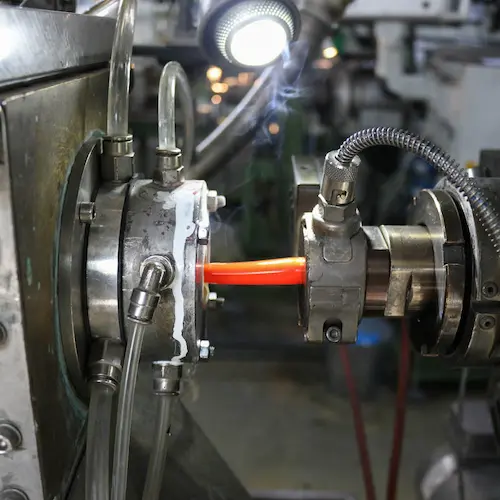
Aufbau und Arten von Extrudern
Schneckenextruder
Die wohl am weitesten verbreitete Variante der Extruder sind Schneckenextruder. Bei einem Schneckenextruder wird das Material auf eine Förderschnecke gegeben, die verschiedene Heizzonen durchläuft. Während die Förderschnecke den Rohstoff nach vorne transportiert, wird dieser in den Heizzonen erhitzt und dadurch weich gemacht. Schlussendlich presst die Schnecke das erhitzte Material aus der formgebenden Öffnung und das Extrudat wird durch Abkühlung, die meist in einem Wasserbad stattfindet, in der gewünschten Form ausgehärtet. Für viele Anwendungen in der Kunststoff- und Lebensmittelindustrie sind die einfach aufgebauten, robusten und vergleichsweise kostengünstigen Einschneckenextruder die effizienteste Alternative.

Neben den einfachen Einschneckenextrudern, die, wie der Name bereits vermuten lässt, nur eine Förderschnecke besitzen, finden häufig auch Doppelschneckenextruder Anwendung. Bei Doppelschneckenextrudern laufen zwei Förderschnecken gleichzeitig entweder gegen- oder gleichläufig, um das Material in Richtung Öffnung zu befördern. Zweischneckenextruder haben vor allem den Vorteil, dass das beförderte Material besser durchmischt wird. Dementsprechend finden diese hauptsächlich bei schwer mischbaren Materialien Anwendung. Zudem sorgen Doppelschneckenextruder im Vergleich zu Einschneckenextrudern für eine gleichmäßigere Materialförderung, was bei schwierig zu verarbeitenden Materialien zu einer höheren Prozesssicherheit führen kann.
Kolbenextruder
Auch bei einem Kolbenextruder wird formbares Material durch eine formgebende Öffnung gepresst. Allerdings wird bei dieser Art der Extrusion das Rohmaterial in einen Zylinder gegeben, in dem sich der Kolben befindet. Durch gleichmäßigen Druck des Kolbens wird das Material dann in Richtung der Öffnung befördert. Die Extrusion mit Kolbenextrudern findet vor allem in Bereichen Anwendung, die eine hohe Präzision erfordern. Zusätzlich bietet sich das Verfahren bei Rohstoffen an, die unter hohem Druck verarbeitet werden müssen.
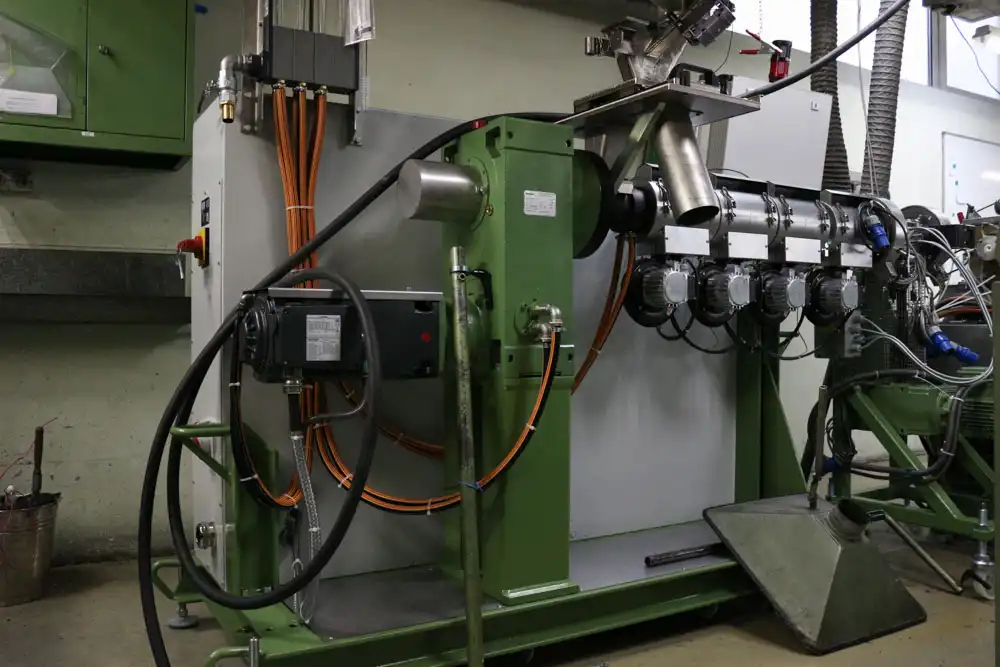
Schneckenextruder vs. Kolbenextruder
Sowohl die Extrusion mit Schneckenextrudern, als auch die mit Kolbenextrudern hat ihre Vor- und Nachteile. Der wohl größte Unterschied der beiden Extrusionsarten ist die Kontinuität. Während bei Schneckenextrudern sehr lange am Stück produziert werden kann (die Anlagen müssen nur zur Reinigung oder zum Materialwechsel abgestellt werden), muss die Produktion mit Kolbenextrudern im Vergleich deutlich häufiger unterbrochen werden. Der Grund dafür ist simpel: Der Kolben muss immer wieder zurückgezogen und der Zylinder neu mit Material befüllt werden. Beim Schneckenextruder hingegen kann das Material kontinuierlich, durch Zugabe auf die sich drehende Schnecke, befördert werden.
Mit dieser Methode erreichen Schneckenextruder in der Regel einen deutlich höheren Materialdurchsatz als Kolbenextruder. Auf der anderen Seite sind Kolbenextruder in der Lage, deutlich höhere Drücke zu erzeugen als Schneckenextruder, was bei der Extrusion einiger Materialien von Vorteil sein kann. Zudem sind Kolbenextruder aufgrund ihres vergleichsweise simplen Aufbaus einfacher zu warten und zu reinigen als die deutlich komplexeren Schneckenextruder.
Während Schneckenextruder das verarbeitete Material bei der Förderung durch die Drehbewegung zusätzlich durchmischen, passiert das bei Kolbenextrudern kaum. Jedoch entsteht durch diese Bewegung auch eine hohe Materialbelastung aufgrund von Scherkräften. Hier kann wiederum der Kolbenextruder punkten, bei dem diese Scherkräfte nicht auftreten und das Material somit schonender befördert wird.
Unter dem Strich gibt es also nicht für alle Materialien den perfekten Extruder. Es muss im Einzelfall entschieden werden, welcher besser zum angestrebten Ergebnis passt. Die Vor- und Nachteile von Schnecken- und Kolbenextrudern noch einmal im Überblick:
Schneckenextruder | Kolbenextruder |
+ Kontinuierlicher Betrieb | + Besonders hoher Druck möglich |
+ Hohe Durchsatzrate | + Präzise Dosierung |
+ Vielseitige Anwendungsmöglichkeiten | + Einfache Reinigung und Wartung |
+ Intensive Materialdurchmischung | + Schonende Materialbehandlung |
– Komplexe Reinigung und Wartung | – Unterbrechung im Betrieb |
– Hohe Materialbelastung | – Geringere Durchsatzrate |
– Begrenzte Anwendungsmöglichkeiten |
Verschiedene Extrusionstechniken
In der über 200-jährigen Geschichte der Verfahrenstechnik sind diverse Formen der Extrusion entstanden, um aus jedem Material die maximale Effizienz herauszuholen. Die im nachfolgenden groben Überblick erwähnten Techniken lassen sich nicht immer eindeutig voneinander abgrenzen und finden teilweise als Mischformen ihre Anwendung:
Verschiedene Temperaturbereiche
Kaltextrusion
Bei der Kaltextrusion werden Materialien, wie es der Name bereits vermuten lässt, bei niedrigen Temperaturen verarbeitet. Meist findet dieser Prozess bei Raumtemperatur statt. Für die Kaltextrusion eignen sich jedoch nur Materialien, die bei solch niedrigen Temperaturen weich genug sind, um eine neue Form anzunehmen. Durch den Wegfall des Erhitzungsprozesses sind deutliche Energieeinsparungen möglich. Auf der anderen Seite muss aufgrund des härteren Zustands der zu verarbeitenden Materialien oftmals deutlich mehr Druck ausgeübt werden. Dadurch ist der Materialverschleiß der Werkzeuge häufig höher.
Warmextrusion
Bei der Warmextrusion werden die verarbeiteten Materialien auf eine höhere Temperatur gebracht. Das ist bei vielen Werkstoffen notwendig, damit sie überhaupt in eine neue Form gepresst werden können. Im Vergleich zur Kaltextrusion muss in vielen Fällen deutlich weniger Druck aufgewendet werden, um das Material durch die Düse zu pressen. Die Warmextrusion findet unterhalb der Rekristallisationstemperatur des verarbeiteten Materials statt. Wird das Material oberhalb der Rekristallisationstemperatur verarbeitet, spricht man nicht mehr von einer Warmextrusion, sondern von einer „heißen Extrusion“.
Verschiedene Druckvarianten
Direkte Extrusion
Bei der direkten Extrusion wird, wie in den meisten bisher beschriebenen Beispielen, ein Material durch eine Düse gepresst und erhält dadurch seine Form. Dadurch entsteht allerdings Reibung am verarbeiteten Material, was sich in bestimmten Fällen negativ auf die Eigenschaften des Endproduktes auswirken kann.
Indirekte Extrusion
Der große Unterschied der indirekten Extrusion gegenüber der direkten Extrusion ist, dass das Rohmaterial fest in einer Kammer verbleibt. Die Formgebung passiert dadurch, dass sich die Düse auf das Material zubewegt und es hierdurch durch die Öffnung in Form gepresst wird. Das hat den Vorteil, dass die Reibung, die bei der direkten Extrusion durch das Gleiten des Rohmaterials in Richtung Düse erzeugt wird, wegfällt.
Hydrostatische Extrusion
Bei der hydrostatischen Extrusion wird das verarbeitete Material nicht direkt mittels eines Kolbens durch eine Öffnung gepresst, sondern es wird eine Flüssigkeit zwischen Material und Kolben hinzugefügt. Das hat den Vorteil, dass sich der Druck des Kolbens gleichmäßiger verteilt. Zudem ist die Reibung durch die Verwendung von Flüssigkeiten deutlich geringer.
Impact Extrusion
Bei der Impact Extrusion wird ein kurzer Schlag eines Stempels verwendet, um das Material zu formen. Dabei entsteht im letztendlich geformten Werkstück ein Hohlraum, indem sich das Material durch den Schlag um den Stempel schließt.
Anwendungsgebiete der Extrusion
Extrusion in der Kunststoffverarbeitung
In der Kunststoffverarbeitung ist die Extrusion eine bedeutende Verfahrenstechnik für die Formgebung von Thermoplasten. Thermoplaste eignen sich besonders gut für die Herstellung von Extrudaten, da sie unter Hitzeeinfluss weich und verformbar werden. Dadurch lassen sie sich mittels der Schnecken oder Kolben perfekt durch eine Düse in eine bestimmte Form pressen. Danach können die Thermoplaste durch Kühlstrecken in ihrer neuen Form fixiert werden. Kunststoffe sind zudem, oftmals in Form von Granulaten, perfekt für die Verarbeitung in einem Extruder portionierbar. In der Kunststoffverarbeitung bietet die Extrusion unter anderem folgende Vorteile:
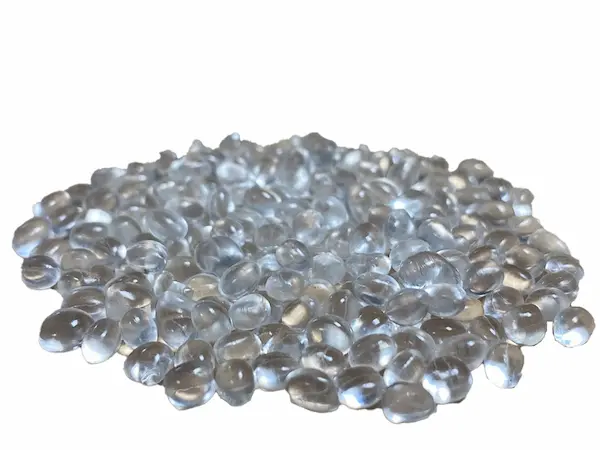
- Hohe Prozessgeschwindigkeit: Es können, gerade bei der Verwendung von Schneckenextrudern, große Mengen ohne Unterbrechungen produziert werden.
- Material- und Kosteneffizienz: Dadurch, dass die Maschinen nur selten abgestellt werden müssen, entsteht im Vergleich zu anderen Verfahrenstechniken zur Formgebung von Kunststoffen wenig Abfall. In Kombination mit den hohen Durchsatzraten macht das die Extrusion auch kosteneffizient.
- Vielseitigkeit: Mittels unterschiedlicher Extruder (vor allem die Düse ist wichtig) lassen sich diverse Formen mit einer hohen Prozesssicherheit realisieren.
Beispiele für Kunststoffextrudate
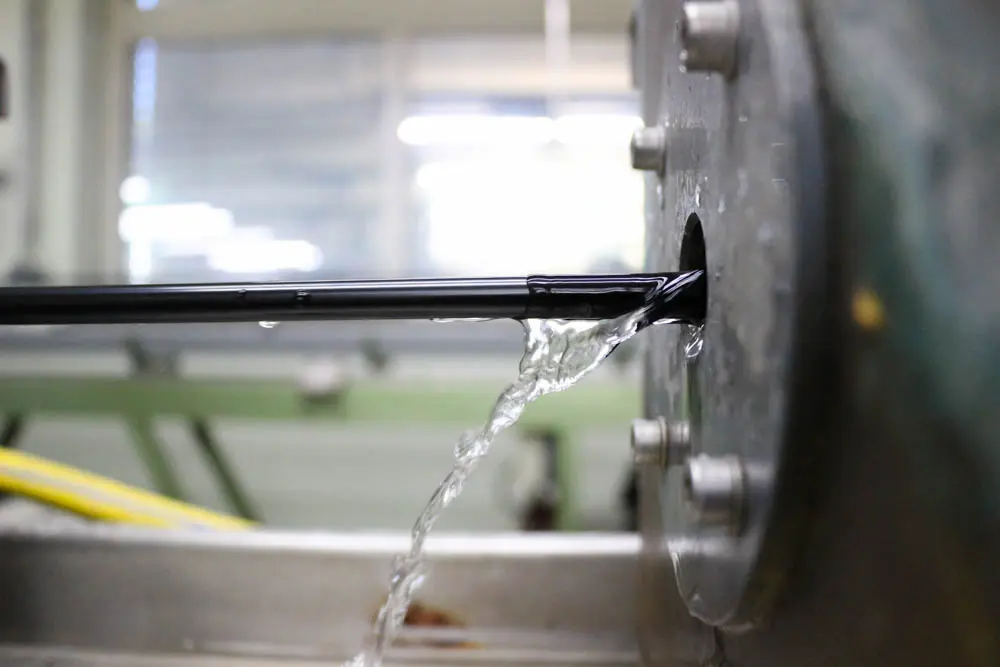
- Schlauchextrusion: Industrieschläuche lassen sich in diversen Formen extrudieren. Dabei wird der Kunststoff, in vielen Fällen Polyurethan oder Polyamid, wie gehabt durch eine Düse gepresst. Ein sogenannter Dorn in der Mitte der Düse sorgt dafür, dass der Schlauch hohl bleibt. Die so produzierten Extrudate finden oftmals als Pneumatikschläuche oder zum Transport von flüssigen Medien ihren Einsatz.
- Folienextrusion: Bei der Folienextrusion wird das Kunststoffgranulat durch eine extrem schmale Düse (Schlitzdüse) gepresst. Dadurch lassen sich sehr dünne Kunststofffolien ohne Unterbrechung produzieren und auf Rollen aufwickeln.
- Profil- und Plattenextrusion: Auch komplexe Profile, beispielsweise für die Bau- oder Möbelindustrie, lassen sich mittels Extrusion herstellen.
- Faserextrusion: Synthetische Fasern für Textilien oder Teppiche lassen sich ebenfalls extrudieren. Dafür wird der Kunststoff durch sehr feine Mehrlochdüsen (Spinndüsen) gepresst, um eine Vielzahl an Fasern gleichzeitig herstellen zu können.
Extrusion in der Metallverarbeitung
Die Extrusion wird bis heute, so wie es der als Erfinder des Prozesses geltende Bramah im Sinn hatte, in der Metallverarbeitung eingesetzt. Die Grundprinzipien der Verfahrenstechnik sind in Kunststoff- und Metallverarbeitung ähnlich: Die Metalle werden verformbar gemacht und durch eine Öffnung in die gewünschte Gestalt gepresst. Allerdings unterscheiden sich die spezifischen Verfahren aufgrund der unterschiedlichen physikalischen Eigenschaften deutlich. Allein die Verarbeitungstemperaturen sind in der Metallverarbeitung deutlich höher.
Beispiele für Metallextrudate:
- Profile und Stäbe: Aluminiumprofile beispielsweise für Fensterrahmen, Türrahmen oder für den Fahrzeugbau lassen sich mittels der Extrusion kontinuierlich fertigen.
- Drähte: Elektrische Leitungen und Kontakte aus Kupfer sind in vielen Fällen klassische Extrudate.
- Rohre: Die älteste Anwendung der Extrusion hat bis heute Bestand. Rohre aus diversen Metallen werden extrudiert. Der größte Vorteil hierbei ist die nahtlose Fertigung.
Extrusion in der Lebensmitteltechnik
Anders als man intuitiv vielleicht vermuten möchte, kommt die Extrusion oft auch in der Lebensmittelindustrie zum Einsatz. Vier Gründe, die zum Einsatz der Extrusion in der Lebensmittelindustrie beitragen, sind:
- Effizienz: Bei der Extrusion können Lebensmittel gleichzeitig gekocht und in Form gebracht werden, was Arbeitsschritte spart und eine besonders effiziente Produktion ermöglicht.
- Qualität: Durch die hohe Prozesssicherheit der Extrusion können große Mengen an Lebensmitteln in einer gleichbleibenden Qualität hergestellt werden.
- Nährstofferhaltung: Der Koch- und Formgebungsprozess kann für die meisten Lebensmittelextrudate so gestaltet werden, dass die Nährstoffe aus den verwendeten Zutaten erhalten bleiben.
- Vielseitigkeit: Durch Extrusion lässt sich eine Vielzahl an Lebensmitteln herstellen.
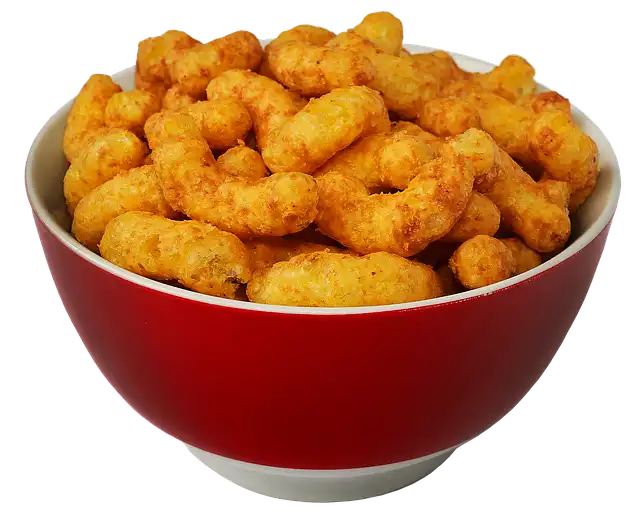
Beispiele für Lebensmittelextrudate
- Snackprodukte: Chips und Flips lassen sich durch Extrusion ideal gleichzeitig garen und in Form pressen.
- Frühstückszerealien: Frühstücksprodukte in verschiedenen Formen wie Cornflakes oder gepuffte Reisflakes lassen sich ebenfalls effizient extrudieren.
- Teigwaren: Durch verschiedene Düsen lassen sich Nudeln in allen Formen und Längen mittels Extrusion herstellen.
- Fleischersatzprodukte: Durch die Extrusion von texturierten Pflanzenproteinen lassen sich vegetarische und vegane Produkte herstellen, die Fleisch in ihrer Textur ähneln.
- Süßwaren: Kaugummi, Geleebonbons und Lakritze erhalten ihre typische Form oftmals mittels Extrusion.
Viele der Produkte, die wir auf täglicher Basis verzehren, werden also mittels des Verfahrens, das am Ende des 18. Jahrhunderts zur Herstellung von Metallrohren entwickelt wurde, in ihre typische Form gebracht. Auch in der Lebensmittelindustrie werden sowohl Kolbenextruder als auch Schneckenextruder in ihren verschiedenen Ausgestaltungen verwendet.
Zusammenfassung
Extrusion wurde bereits Ende des 18. Jahrhunderts als Verfahrenstechnik erfunden und hat sich seitdem enorm weiterentwickelt. Grundsätzlich wird bei der Extrusion ein Material durch eine formgebende Öffnung (Düse) gepresst und erhält dadurch seine finale Gestalt. Der Prozess wird dazu verwendet diverse Rohstoffe wie Metalle, Kunststoffe, aber auch Lebensmittel zu verarbeiten. Einer der Hauptvorteile der Extrusion ist es, dass sich nahtlose Produktionsabläufe realisieren lassen. Darüber hinaus bietet sie eine sehr hohe Prozesssicherheit und eine vergleichsweise hohe Materialeffizienz.
Die für die Extrusion benötigten Geräte nennt man Extruder. Extruder kommen in zahlreichen verschiedenen Formen vor, von denen jeder seine Vor- und Nachteile hat. Hauptsächlich zu unterscheiden sind Schnecken- und Kolbenextruder. Genau wie es verschiedene Arten von Extrudern gibt, kommen auch verschiedene Prozessgestaltungen vor. So gibt es beispielsweise Kalt- und Warmextrusion, aber auch direkte und indirekte Extrusion. Unter dem Strich bietet die Verfahrenstechnik für diverse Branchen eine attraktive Möglichkeit, Rohstoffe in effizienter Manier in die angestrebte Form zu bringen.
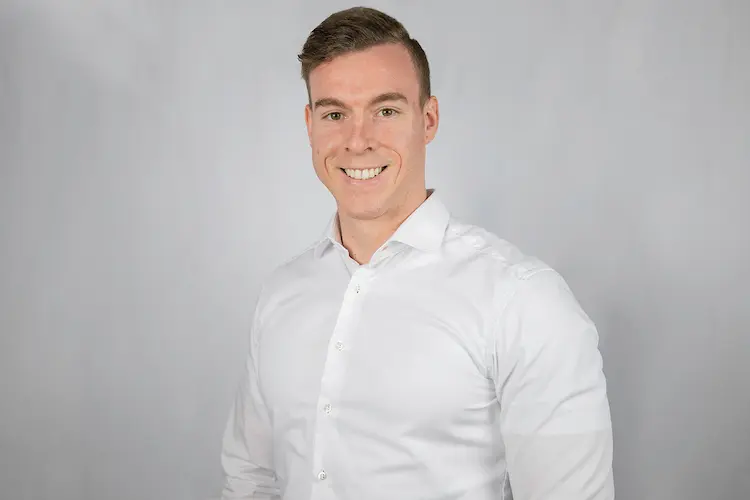
Dan Biebl
Geschäftsführer
Ich hoffe unser Artikel konnte Ihnen weiterhelfen!
Wir bei PAPUREX unterstützen Sie dabei den richtigen Schlauch für Ihre individuelle Anwendungen zu finden. Sie haben noch fragen zum Artikel? Wenden Sie sich gerne an mich!
Per Mail an dan.biebl@papurex.de
Oder per Telefon: 06209 72102 40
Auf der Suche nach Spezialschläuchen?
Kontaktieren Sie uns gerne! Egal ob per Mail oder Telefon, unsere Experten sind für Sie da.